Acerca de

Indo performs the first step with unprocessed bales and rolls of yarn where cotton lints are fed into the machine to be well mixed and reduced to the minimum possible size. This is a section in which the supplied compressed bales are opened, cleaned & blended, or mixed to form a uniform lap of a specific length. It is equipped with the latest world-class vision shield contamination remover (Vetal Scan). The cleaning efficiency of the blow room is 50 to 70%.
carding
Laps are fed into the machine parallelly and fibre to fibre separation is achieved in this process to provide uniformity. The spiked teeth in the machine help in removing impurities. The output includes thin parallel sheets called webs. These webs are put into funnels to make it into slivers.
Thereafter, the sliver is sent to an open-end spinning machine such as rotor spinning or air jet spinning to provide us with open-end yarn. If not, the sliver goes through the following processes.

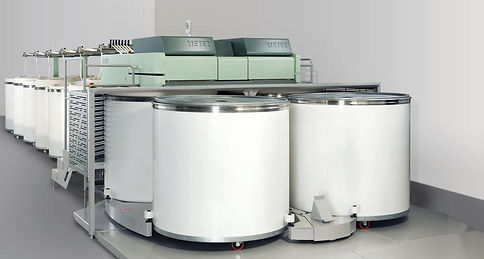
draw frames
(Drawing)
In the preceding process, the output consists of a longer and thinner sliver formed as a result of a number of slivers being passed through the carding machine. In order to achieve a perfect evenness in a sliver, it is passed through several draw frame rollers at different speed. Also, with the appropriate suction removal systems, 80% of the dust present in the fibre is withdrawn.

lap former
(super lapping)
The lap former has the charge of developing the laps that is engaged to feed the comber machine. There are three creels on the machine, three different zone arrangements and three diverse feed plates in this machine.
A lap of width 30 to 40 inches and thickness of 1 inch is wound onto a bobbin.


combing
The process of combing is essential only if there is a specific requirement for a finer or smoother yarn. The processed sliver processed from the lap former is fed into the combing machine. In this process, the short fibres known as Noils (up to 12 mm. long) are eliminated. Maximum fibre straightening is achieved by this process.

Ring frame
(Spinning & twisting)
The processed roving bobbins are fed into the ring frame. High speed twists are inserted in the yarn with the help of a ring traveller. This process helps in the completion of yarn manufacture. After the yarn is wound on ring bobbins, it is sent for quality control.

simplex
(roving)
After being fed into this machine, the comb sliver is drawn many times to its original length until it reduces to a diameter of a pencil lead maintaining the integrity of the draft strands. During this passage, three works are done on the sliver: drafting, twisting and winding.
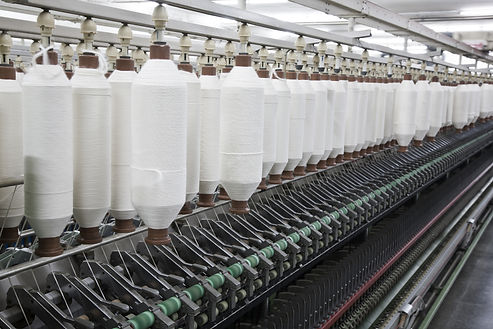

Autoconer
To ensure resource-saving production, the autoconer is highly automated. It winds spun cotton yarn from the ring bobbins to cones, analysing it as it winds. Usually, 50 to 60 breaks per lakh metre faults are detected and cleared with our latest high-tech yarn clearers. Uniformity is achieved after joining the ends by the method of splicing, where the ends are opened, mingled and reformed. All knots are eliminated here.
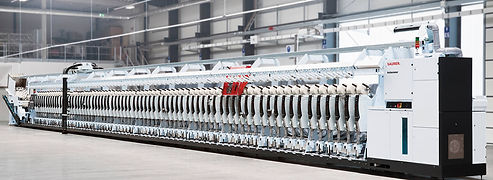

UV INSPECTION & YARN CONDITIONING
100% UV lamp checking of the cone is practiced to ascertain any variation.
Then, the yarn is humidified at about 6% to 8% with our perforated tubes, plastic, paper or from the inside by dosing an exact quantity of moisture.
The machine moistens the cones with an amount of prefixed and adjustable moisture on the cones itself.
This operation allows to retain desired humidity into the cone before dispatch and gives it a greater tenacity and flexibility in slippage of the yarn.

Packaging
The packaging is done to protect the yarn during distribution, storage, sales and end-use. We optimize the cost, while considering the aspects of structural design, quality assurance, regulatory guidelines, end-use by the customer and minimal wastage of packaging materials.
According to the customer requirements, the cones are packed in one of the three forms i.e bag, carton or pallet.

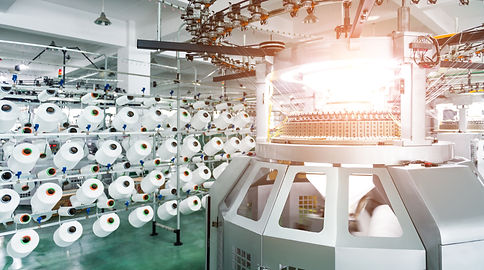
Knitting
We use a series of needles to interlock loops of yarn to construct a type of fabric. Our knitting machine works over one million stitches a minute set to drop or add stitches automatically narrowing or widening the fabric at certain points as per
the requirement.
Single jersey, Rib and interlock are the types of knits we manufacture for 100% cotton yarn.

Weaving
There is a total elimination of any spooling operation. The fact that these machines work at high speed gives us a capacity to increase production whenever there is an increase in demand. Our machinery makes the woven fabrics dimensionally stable in nature which do not unravel when you cut them.
